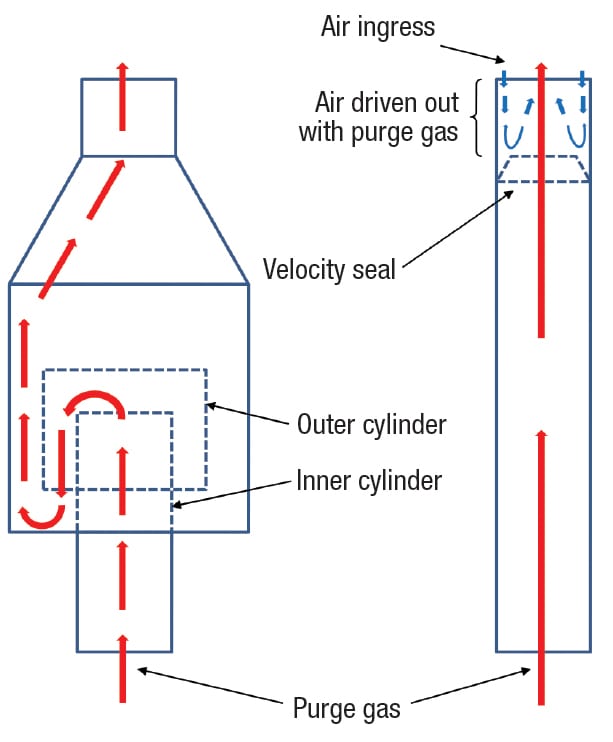
Flare sweep gas means the gas intentionally introduced into the flare header system to maintain a constant flow of gas through the flare header to prevent oxygen buildup in the flare header and for a flare without a flare gas recovery system to prevent oxygen infiltration. To access the working calculator please sign up for free membership trial.
Some of the data you require for these calculations are.
Flare purge gas calculation. Flare Purge Gas Calculator. This is a sample of the Flare Purge Gas Calculator. To access the working calculator please sign up for free membership trial.
Purge gas flow requirement calculator to determine the minimum required continuous purge gas flow in a flare stack to avoid air ingress into the flare stack. The purge gas flow calculation is based on the guidelines from API standard 521. API standard 521 describes the equation to determine minimum purge gas flow requirement for a flare stack of given diameter and given composition of the continuous purge gas flow.
Another ways to avoid ingress into the flare stack flare KO drum flare network are - liquid seal flame arresters etc. Although flame arresters are not frequently used due to possibility of obstruction in. If a mass flow meter is used you must also measure molecular weight and convert the mass flow to a volumetric flow as follows.
FlareMMscf 0000001 Flarekg MVCMW p where MVC is the molar volume conversion factor 8495 scfkg-mole at 68 F and 147 psia or 8366 scfkg-mole at 60 F and 147 psia depending on the standard conditions used when determining HHV p and MW p is. Some of the data you require for these calculations are. - average molecular weight of purge gas.
-
whether or not any seals are present in the system ie. Molecular seal liquid seal or velocity seal. - Size of the flare header.
-
presence of hydrogen that changes everything as the burning velocity is very very fast. If the gas is multicomponent Husas formula becomes a little top heavy and I recommend using Fb 625 1 - 075MW289615 MW Mol wt of purge gas mixture In the same discussion thread there was a quote from API RP 521. Alternatively the continuous introduction of purge gas can be used to prevent flashback.
Limits minimum heat content of flare gas. 200 BTUscf for non-assist flare 300 BTUscf for assist flare Maximum exit velocity based on heat content of flare gas 60 400 FPS Flame may not always be visible Hydrogen Low BTU gas - eg. NHV CZ Net Heating Value of the Combustion Zone Gas NHV LFL Net Heating Value of the Flare Vent Gas if Diluted to the Lower Flammability Limit NHV VG Net Heating Value of the Flare Vent Gas NHV VG-LFL Net Heating Value of the Flare Vent Gas if Diluted to the Lower Flammability Limit NSPS New Source Performance Standards.
For periods when there is no assist steam flow or premix assist air flow NHV cz NHV vg. N H V c z Q v g N H V v g Q v g Q s Q a. NHV cz Net heating value of combustion zone gas Btuscf.
NHV vg Net heating value of flare vent gas for the 15-minute block period Btuscf. Header end and emergency gas purge Flare risers tips and associated hardware fuel gas ignition steam or air Associated monitoring and safety systems including infra red monitors. Milton Keynes Flare System Design for Oil and Gas Installations Onshore Flare System.
The flare headers should be continuously purged with fuel gas. The purge rate should be at least the minimum required to guarantee that air ingress into the tip is prevented. Purge flow rates should be measured at each purge point by a flowmeter.
A no flow alarm should be provided on each flowmeter. When the first baffleseal diameter ratio is d 1 D 092 and hydrocarbons are discharged in the flare the minimum safe purge gas flow rate is 005 ms. However when the hydrogen content in the discharge gas is high the minimum safe purge rate is higher.
When the first baffleseal diameter ratio is d 1D 092 and hydrocarbons are discharged in the flare the minimum safe purge gas flow rate is 005 ms. However when the hydrogen content in the. What is Purge Gas.
Purge gas or purge flow is required to prevent air impingement in the process header when there is little or no process flow going to the flare as in the case of a dedicated intermittent or ESD flare. Should air enter the flare stack a release of process gas could result in a combustible mixture present within the. The function of flare purge gas is performed by flare sweep gas.
Flare sweep gas means the gas intentionally introduced into the flare header system to maintain a constant flow of gas through the flare header to prevent oxygen buildup in the flare header and for a flare without a flare gas recovery system to prevent oxygen infiltration. The quantity of inert gas required for each cycle is P-1 vessel volumes. Let say you want to purge a vessel from 21-mole oxygen to 1-mole oxygen.
You use inert gas to pressure to 5 atm. Guess number of cycle. We guess 2 cycles for started.
1-P n 15 2 004. 004 x 21-mole 084-mole. The results is satisfied.
Low-pressure flare tips are sized for 05 Mach for a peak short-term infrequent flow emergency release and 02 Mach for normal conditions where Mach equals the ratio of vapor velocity to sonic velocity in that vapor at the same temperature and pressure and is dimensionless. ANALYSIS OF TCEQ FLARE STUDY RESULTS Analyzed data for the air assisted flare as being more representative of flares used in oil and natural gas production. Report Table 9-1 provides a detailed list of hydrocarbon emissions found in flare plume of an air-assisted flare burning a propylenenatural gas.
Of flare gas recovery and flaring events 1995 to 2006 a discussion of flaring that may continue to occur for safety and environmental reasons and a review of the refinerys ongoing flare.