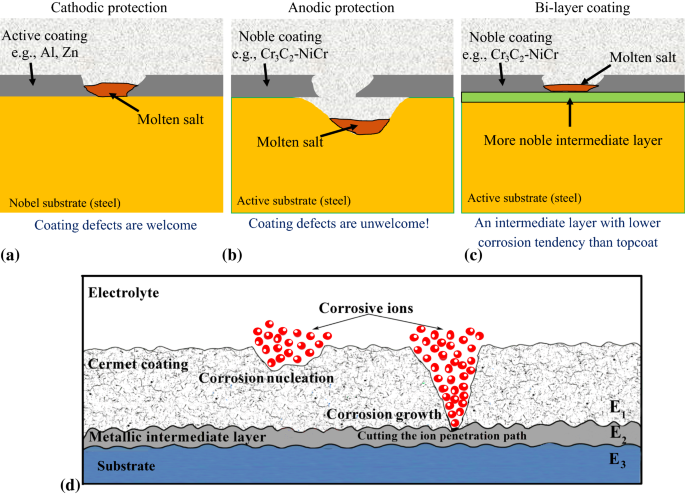
CORROSION RESISTANT COATING The homogeneous nanostructure of Hardide coatings has a volume porosity of. Thermal spray coatings can be an excellent application for providing protection against corrosion.
Master Bond compounds are typically used for corrosion control for.
Corrosion resistant spray coatings. However detonation D-Gun sprayed or high velocity oxy-fuel HVOF sprayed Cr 3 C 2 NiCr and Ni20Cr coatings have 20 to 36 times higher erosioncorrosion resistance than the plasma sprayed NiCr and stellite-6 coatings and retain their erosioncorrosion resistance properties. This review aims to present a comprehensive state-of-the-art overview of the essential concepts in high-temperature corrosion-resistant coatings particularly the coatings deposited by thermal spray techniques. The review takes a holistic approach to the relevant topics at time being concise and critical with a primary focus on the key developments including the challenges and opportunities with thermal spray coatings.
An effective corrosion resistant spray coating provides corrosion protection and adhesion while proving resistant to fatigue and exposure to water. The best spray coatings for many industrial applications are long-lasting easy to apply cost effective and high performance without leading to adverse environmental reactions. With our systems tanks and equipment can be returned to service.
Metal coating and WC coating material selection for thermally sprayed corrosion erosion and abrasion resistant coatings. High bond strength hot corrosion resistance ductility fracture toughness. How to choose carbide metal or alloy coating to achieve the best coating result.
Weld through the metal coating without cracking or delamination. Corrosion Resistance Thermal Spray Solutions provides corrosion resistant coating solutions. Corrosion can be defined as surface deterioration caused by reaction to harsh environmental conditions oxidation or chemical action.
Thermal spray coatings can be an excellent application for providing protection against corrosion. The cold spray process is applicable to corrosion-resistant coatings zinc and aluminum dimensional restoration and repair nickel stainless steel titanium and aluminum wear-resistant coatings chromium carbide nickel chromium tungsten carbide cobalt and tungsten copper electromagnetic interference EMI shielding of components and structures high strength dissimilar material coatings for unique. Benefits of Corrosion Protection Coatings.
The main benefits of corrosion protection include high wear resistant lengthening the service lifespan as well as better protection against aggressive environments such as immersion in sea water. Corrosion is a huge issue for steel products and that is why you will see corrosion protection coatings used for endless applications across all industries. AA Coatings a US Navy approved surface engineering company recommends thermal spray coatings for a number of structural components such as wind turbines bridges large pipelines and ship structures with the last two being over-exposed to saltwater induced corrosion.
These coatings are also applicable for building corrosion resistance in valve bodies pump housings. Corrosion is a natural chemical reaction in which metals transform into more chemically stable forms such as oxides hydroxides or sulfides. Most often this occurs in machine components we they come into contact with water or corrosive chemicals.
Corrosion resistant coatings create a surface barrier of nickel alloys such as Inconel or chromium alloys such as molybdenum or zirconium. Thermal spray coatings differ from traditional coatings paints epoxies etc in that they offer higher temperature resistance superior corrosion and wear resistance and a longer life. Coating materials can be selected for extreme industrial environments atmospheric corrosion or for purely decorative reasons.
Thermal spray coatings may be applied in the shop using manual or automated. The protection of carbon steel against corrosion in marine environment by metallic coatings obtained from thermal spray process has been used in the last years. However the increasing aggressiveness of new oil and gas wells mainly in the Brazilian pre-salt region of ultra-deep exploitation represents a challenging situation to traditional materials such as carbon steels.
Therefore offshore industry has increased the use of thermal spray. Serious problems due to high temperature corrosion. Thermal spray coatings can offer an attractive solution for corrosion protection of boiler tubing.
The objective of this work was to determine the corrosion resistance of thermal spray coatings in biomass combustion conditions. The research focused mainly on improving the high temperature. High-Temperature Anti-Oxidizing Corrosion Resistant Ceramic Composite Coating for Aircraft Engine Components.
Because of its high temperature capabilities it offers excellent protection when exposed to cyclic high temperature and corrosive salt environments continuing to provide sacrificial properties at temperatures to 1150F. Hot spray coating. Thermal spraying as well as diffusion coating.
New thermal spray technologies are being adopted for producing stronger abrasion-resistant coatings HVAF and HFPD for example. However the frictional wear versus corrosion resistance needs to. Corrosion Resistant Spray Coating Systems Spray Quip provides a variety of single and multiple component coating solutions accesories from brands like Graco Binks WIWA Wagner etc.
Whether fighting or attempting to prevent rust and corrosion applying multiple-component coatings or transferring liquids we can supply you with the protective coating equipment that will match your. Master Bond compounds are typically used for corrosion control for. Elevated temperature resistant high build solvent free coatings are available to repair and prevent corrosion under insulation CUI.
Water penetration from rain wash downs and condensation is hard to detect. Trapped water can lead to unexpected downtime costly equipment overhauls and operation disruptions. CORROSION RESISTANT COATING The homogeneous nanostructure of Hardide coatings has a volume porosity of.
Two of the most common corrosion resistant coatings are ECTFE also known by the trade name Halar and ETFE also known by the trade name Tefcel. Halar is an excellent abrasion resistant coating and has very high thermal insulation properties.