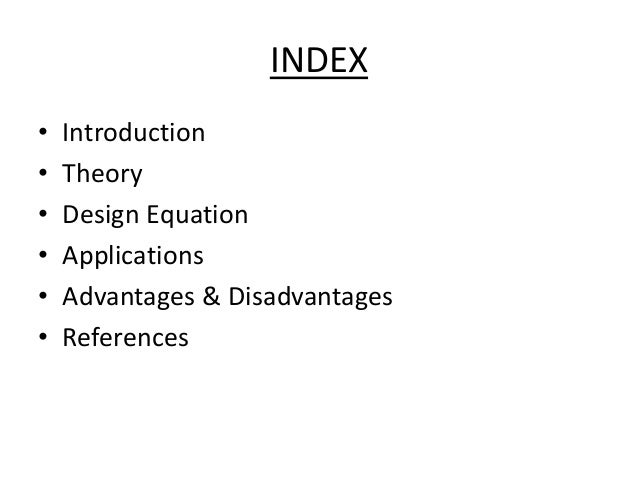
Maintenance costs are lower. They consist of vessels usually cylindrical in which.
Advantages compared to stirred reactors include low capital and energy cost lack of moving parts and satisfactory heartand mass transfer performance ease of scale-up low shear characteristics etc.
Advantages and disadvantages of bubble column reactor. Some of the disadvantages of bubble columns are backmixing in liquid phase may result in lower conversion and unfavorable selectivity and limitations on catalyst size and loading. Despite their simple operation bubble column reactors exhibit some of the most complex hydrodynamics due to spatiotemporal variations in interactions among gas liquid and solid phases. Bubble columns are intensively used as multiphase contactors and reactors in chemical biochemical and petrochemical industries.
They provide several advantages during operation and maintenance such as high heat and mass transfer rates compactness and low operating and. This type of reactor has advantages of higher mass transfer rates and low operational and maintenance costs due to fewer moving parts. The bubble column reactor has been regarded as an attractive system for large-scale gas fermentations.
Bubble columns are intensively used as multiphase contactors and reactors in chemical biochemical and petrochemical industries. They provide several advantages during operation and. Maintenance costs are lower.
Bubble columns and airlift loop reactors can be built with much larger working volumes than stirred tank reactors. Their advantages become effective predominantly at scales larger than 50-100 m³. Here we focus the attention on the dynamics of bubble columns and explain the fluid mixing in the turbulent flows in.
With your needrequest We will collect and show specific information of advantages and disadvantages of bubble column reactor ppts within short timeSo hurry to Ask now No Registration No fees its a free service from our sideOur experts are ready to help you. Bubble column reactors are multiphase contactors that have found several industrial applications owing to various attractive features including excellent thermal management low maintenance cost. Due to various advantages such as simple geometry ease of operation low operating and maintenance costs excellent heat and mass transfer characteristics bubble column reactors are frequently used in chemical petrochemical biochemical pharmaceutical metallurgical industries for a variety of processes ie.
Hydrogenation oxidation chlorination alkylation chemical gas cleaning various bio-technological. Both advantages and disadvantages of these types of reactors are presented. Key parameters related to the performance of bubble column reactors are also presented.
In addition in Chapter 1 a brief literature review is presented on both experimental and numerical techniques utilized in investigations on the performance of bubble column reactors during the past decades. These reactors are structurally very simple. Advantages compared to stirred reactors include low capital and energy cost lack of moving parts and satisfactory heartand mass transfer performance ease of scale-up low shear characteristics etc.
Bubble column reactors are characterized by a high liquid content and a moderate phase boundary surface. The bubble column is particularly useful in reactions where the gas-liquid reaction is slow in relation to the absorption rate. This is the case for gas-liquid reactions with a Hatta number Ha.
It needs reliable similarity criteria that would result in similar mixing and hydrodynamics and hence transport and performance in two different scales. Numerous experimental and computational studies have been performed to investigate the flow behavior of bubble column reactors for a proper design and scale-up. Bubble-column reactors BCRs are gaining an important place in both chemical and biochemical industries 3.
Unlike mechanically agitated reactors bubble columns are simple to construct and operate. They consist of vessels usually cylindrical in which. Diagram of the bubble column reactor for ozonation studies.
The diameter of the reactor is 19cm with a total volume of 1032L. The volume of the gas-mixing chamber is 255L. The capillaries are 14cm long with an inner diameter of 04mm.
They are disposed uniformly distributed at the bottom of the reactor with 21cm of separation. DCb At dt DAa. Dhotre MT Joshi JB 2004 Two-Dimensional CFD Model for the Prediction of Flow Pattern Pressure Drop and Heat Transfer Coefficient in Bubble Column Reactors.
Chemical Engineering Research and Design 82A6689-707. Bubble Column ReactorBubble columns are mainly continuously operating three-phase reactors. The reactant liquid contains suspension catalyst particles in a bubble column reactor is stirred by the reactant gas introduced continuously through a gas distributor installed at the bottom of the reactor such nozzles perforated plates sparger or tubes.